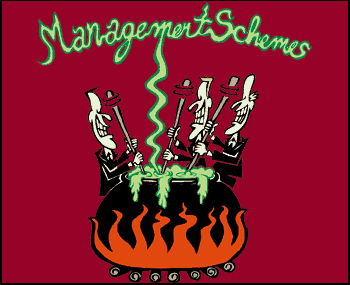
Management Schemes – A Short History
At some point all union leaders are faced with a proposal or announcement from management that they will be implementing a "new system" at the workplace. This "system" might be one of any listed above or have a totally different name. Whenever and however this announcement comes, it means that the Union must put on its thinking cap and be ready to get the members involved.
What does management really want?
This is one of the key questions the union must figure out.
In the case of "for profit" employers it is always safest to assume that management wants to increase profits. There are many ways for them to do this, but it usually involves having workers work harder and producing more with fewer people.
In the case of "non-profit" employers it is safe to assume that they want to make themselves look better (and maybe get themselves a pay raise) by having fewer employees doing more work.
If the union starts with these basic assumptions, then it is easier to figure out the actual details of how these "new systems" will work.
In some rare cases the employer doesn't want to implement these programs but is being forced to by larger customer. Some companies will insist that their suppliers all institute ISO 9000 (or ISO 14000 etc.) or have workplace teams. Part of the job of the union is to figure out if the boss really wants to implement these programs or are they just "window dressing" for their customers. Figuring out the answer to this question will help the union decide its strategy.
Two kinds of employer schemes
Many Different Names
- Kaizan
- Workout
- ISO9000, 14,000 etc.
- Direct Flow Technology
- Just in Time
- Cell Manufacturing
- Win-Win Bargaining
- Quality Circles
- Self Directed Workforce
- High Performance Workplace
- Worker Empowerment
- Six Sigma
- OSHA Exemption
- Statistical Process Control
- Team Concept
- Lean Manufacturing
One type strives to get the workers, with or without the union, to act in groups to help management improve productivity. These are sort of brainwashing sessions. They strive to get workers to think like a boss and to come up with ideas on how to cut other workers, speed-up production and ways to do more work. Quality Circles, Team Concept, Kaizan, fit into this category. These schemes also try to undermine the union by setting up non-union committees that will "make decisions for the workers."
A second employer scheme is usually tied to changes in how production or the work is organized. This could be Cell Manufacturing, Just in Time, Direct Flow Technology, Pay for Knowledge etc. These changes can have a direct effect on parts of the contract. Seniority, layoff and recall procedures, pay grades, transfers, all can be affected. This also gives the union some power, because in most cases the employer cannot make changes to the contract without the union membership's approval.
In non-profit workplaces this might take the form of setting limits on how long workers can talk to their clients, or setting standardized goals that must be met regardless of the individual situation. In one welfare office this "new system" meant workers could only talk to a client for 2 minutes on the phone, meet with them for 10 minutes, and no client could be kept waiting more then 11 minutes. They had to meet with 6 clients per hour.
Of course many of these employer schemes combine elements of both systems.
Where do these programs come from?
Most of these programs are based upon the work of Frederick Winslow Taylor, who is credited with developing "scientific management."
Taylor started life as an apprentice machinist in 1874 at a small machine shop in Philadelphia. He then went to work in at the Midvale Steel Works in PA. He became a pattern maker, then leadman, foreman and a then an engineer. In his role as an engineer for Midvale Steel and then for Bethlehem Steel Co., he developed his system of workplace engineering that he called "scientific management." To most workers his system became known as "Taylorism." In 1895 he presented his first paper to the American Society of Engineers called "A Piece Rate System." This was followed with "Shop Management" in 1903 and "The Principles of Scientific Management" in 1911.
His studies and theories in various forms became the guiding light for the development of manufacturing in the United States and continue to influence much of managements' philosophy.
Taylor's philosophy and system rested on several ideas:
- If workers had unions that was OK, but the unions and workers had to be convinced that their goals and management's goals were the same; a successful company meant successful workers. He said that union members that felt the boss was their enemy were misguided. Taylor felt that increasing production would lead to more, not fewer workers.
- Workers naturally work slower than they are capable of working, some because they are lazy and most because they believe this will save jobs.
"When the same workman returns to work on the following day, instead of using every effort to turn out the largest possible amount of work, in a majority of the cases this man deliberately plans to do as little as he safely can-to turn out far less work than he is well able to do-in many instances to do not more than one-third to one-half of a proper days work.
- Management could & must "scientifically" study work in order to determine what workers actually could produce, in order to make them produce the maximum amount. Taylor time-studied and compiled statistics on thousands of workers movements thus beginning "pre-determined time study." By breaking a worker's every motion down into basic elements, Taylor could figure out how much a worker could actually produce.
- Management, i.e. engineers, must learn and plan jobs, not the workers. As a skilled machinist Taylor knew that the workers knew more than management. He said that management must take back this knowledge.
"The managers assume for instance, the burden of gathering together all of the traditional knowledge which in the past has been possessed by the workmen and then of classifying, tabulating, and reducing this knowledge to rules, laws, and formulae which are immensely helpful to the workmen in doing their daily work."
- Incentive and piecework systems were needed in order to get workers to stop "soldiering" and produce to the maximum potential. Taylor recommended a 30 percent bonus for most jobs but up to a hundred per cent bonus for very skilled or very demanding jobs. Taylor, anticipating what he knew would happen, said management was foolish if they cut piece rates after workers began producing more, but we all know that is what management always does.
The basics of Taylorism remain intact today, even in all the so-called new labor-management cooperation programs, worker empowerment programs, cell manufacturing etc.
- Take away the workers' independent knowledge of production. This is done with computer controlled machines, statistical process control (SPC) programs, and regular time studies. As much as some bosses talk about "empowering workers to make decisions" it is always done in the context of management knowing and planning exactly how production is to be done.
- Convincing workers that their interests are the same as the bosses. Team concept, quality circles are just modern variations of what Taylor said was needed.
Incentive systems to make workers produce to the maximum have been replaced in many places by the "incentive" of work hard or we will move the business overseas.
They Promise us the World
Many of these employer schemes promise the world, but in a very vague way. Do they really mean that workers will finally be listened to? Will the workers actually run the workplace? Will quality really be improved and will junk never again be shipped out? Will job security be really guaranteed? Or will these new systems usher in more layoffs, speed-up, job cuts, and job de-skilling?
In Part Two we take a more detailed look at a number of these schemes, and, in Part Three, we look at how the Union can make a plan to deal with them.