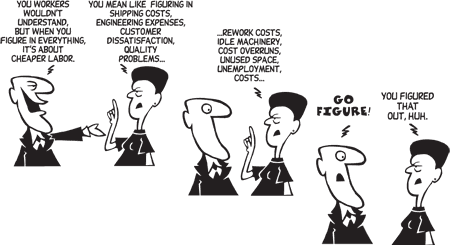
Heres the problem. The Union Committee at Bermuda Taxhaven Inc. is called into the production manager's office. "I just want to give you advance notice that we are going to outsource all the machining work on our Useless Gizmo line. We wont expect any layoffs right away, people will be absorbed on other work but the OT will disappear." Al Ciafarro the Chief Steward asks, "Whats the reason for this?" The plant manager replies, "We can get it done for a lot cheaper and they guarantee the quality." "Can we get copies of all the information, like what it costs to make the Gizmos here and what you will be paying for them?" asks Al. "Well if you are making an official request I guess I have to give it to you, but youll see that were making the right decision."
Heres another situation. The Personnel Manager of the Town of Quincy calls the union into his office. "Youll hear about this anyway so I thought Id tell you first. We are putting out a Request for Bids for someone to run the waste-water treatment plant." Freddy Legomyleg, the Local President says, "You mean youre going to privatize the treatment plant." "Call it what you want, we think we can save the town a lot of money this way. Youll likely all be hired by the new company so you dont have to worry," says the manager. Freddy replies "We would like to see the proposal they will be bidding on and all the information on what it has cost each year for the last two years to run the Treatment plant."
Make or Buy?
In both situations the union knows that they will have a fight. Although there are differences in the situations, one common task will be for the union to analyze the employer's figures and then come up with a proposal of their own. In many private sector cases this is called a "make or buy" situation. That is, can the union prove that they can make the product for the same price it costs the employer to buy the product.
What is the Real Cost of Making a Product or Providing a Service?
This will be the biggest fight and it is key to proving the union's case.
Typically management will give the union a breakdown of the cost per piece that includes the following:
- Wages and Benefits (Labor)
- Materials
- Manufacturing Overhead
- Assessments and Other Costs
Wages and Benefits are usually fairly obvious. If an employee earns $30 per hour in wages and benefits and produces 100 pieces per hour then the wages and benefits per piece are $30 divided by 100, or 30 cents per piece. Be careful that employers dont count some benefits twice, such as computing the yearly cost of benefits, and then adding in an additional figure for vacations.
Materials: These costs can be checked to see if they are accurate.
Manufacturing Overhead: This is usually a fixed figure that they add to everything. It is supposed to cover utilities, maintenance costs, building costs, salaries for non-production workers (white collar, engineering), advertising and many other items.
Assessments and Other Costs: This is a catch-all category that needs to be examined. Many parent companies charge their branch firms a "fee" each year for being allowed to operate. Supposedly this "pays" the parent company for helping them operate. It is really just a way for a parent company to take profits out of a subsidiary but call it something else.
It is in the Manufacturing Overhead and "Other" Category that We Have the Biggest Problem
Here is the problem. The employer will assign a cost per piece based upon all these categories. But in most cases the costs associated with overhead and assessments do not disappear when a company outsources parts. The company still has to pay all the overhead and still has to make payments to the parent company. Even if the management lays off some union members they rarely lay off engineers, white collar etc. They still have to make payments on the building and pay utilities.
Corporate accounting systems that count overhead costs and assessment costs are called "fully allocated cost systems." These are perfectly fair when an employer is trying to calculate what it costs to make products in-house, but unfair when comparing them to what it costs to outsource production.
The accounting system which only looks at costs that will actually change by outsourcing is called a "marginal costing method."
The first task of the union is, therefore, to examine the employer's figures to see if they are using a "fully allocated cost system." This means that they would be including as part of the cost per piece of the items that are manufactured in house, costs that will remain with the company even if they outsource production.
The only real way to make a comparison between products produced in-house and products produced through outsourcing is to only compare what money is REALLY saved, if any.
In many cases once the overhead costs and assessment costs are removed from the figures, the cost per piece of in-house production can be cut by one-third to one-half.
Figuring the Real Costs of Outsourced Parts
Often times management will give the union just one cost for the parts they are outsourcing. They will claim that they have a contract with the outsourcing company that guarantees 100 per cent quality. This may be true but there are still many hidden costs to outsourced parts. Here are some items that may not have been included when the company compared costs. The union should demand the cost of these items and make sure that they are tacked onto the cost per piece of outsourced parts:
1. Shipping and handling costs. Is the supplier providing shipping or does the company have to pay to have the parts shipped? Once the parts are delivered they must be moved into production. These costs (shipping, wages, benefits, overhead etc.) per piece should be added onto the cost of outsourced parts.
2. Legal fees, engineering expenses, negotiation costs. Time and money was spent arranging the outsourcing and negotiating a contract with the outsourcing company. Blueprints had to be made up, specifications arrived at, test programs run with supervision from the company. All these costs must be allocated to the price of outsourcing.
3. Any time, materials, or resources spent on re-working outsourced material that isnt up to quality standards must be included in the cost of outsourced parts. Although the parts are supposed to be 100% good, in real life this never happens. So any time workers spend inspecting parts or having trouble with parts must be charged against the outsourced parts.
4. Idle machinery and idle space does not help pay overhead costs. Therefore overhead costs must be allocated to parts that are outsourced, not shifted onto the parts produced in-house.
Public Sector Hidden Costs
In the public sector, unions have a bit of an advantage in that most data is part of the public record, and therefore the union has a right to see everything. By carefully examining the Request for Bids, and by looking for what is OMITTED, the union can get a clue to the hidden costs of privatization or outsourcing. In the case of the attempted privatization of the waste water treatment plant an examination of the data would show that the town would still have to buy and replace worn or damaged equipment. Since the town would still have these costs, they should be ADDED to any bid made by an outside company. The same is true for maintenance costs. Would the new company have access to using town maintenance employees to repair vehicles or equipment? Who would plow snow in the winter time in the waste water treatment areas? If the town retains these functions, then their costs should be added onto the bid of the new company.
Using Public Hearings
When privatization is threatened there usually must be public hearings, which maybe televised on cable TV. At these hearings the union should come prepared to question the local officials and the companies bidding on the privatization. Ask hard questions like, "How much profit are you guaranteed? Where will this profit come from? What services will you receive from the town? Are you going to cut workers pay and benefits? Are you guaranteeing the facilities will be in the exact same condition when or if they are returned to the town?"
Tips for Stewards
Whenever the union is engaged in a fight against outsourcing or privatization there is one thing that is key, information.
If the employer is bringing in outsourced work then the union needs details on quality, how much time union members spend on re-working parts, moving parts etc. If the employer is contemplating outsourcing or privatization then the union needs detailed information on how the services could be done more efficiently or parts produced more efficiently.
In many cases only the steward is close enough to the action to gather this information over an extended period of time.